ANALISIS PROSES DRAWING UNTUK PEMBUATAN PEDAL BRAKE SEPEDA MOTOR RODA TIGA DENGAN SOFTWARE BERBASIS FEM
Sari
Pedal Brake berfungsi sebagai tempat pijakan kaki pada sistem pengereman pada salah satu produk motor roda tiga di Indonesia. Pembuatan pedal brake menggunakan proses drawing yaitu proses dimana gaya diberikan pada benda kerja agar terdeformasi plastis mengikuti bentuk dari punch dengan kedalaman tertentu. Dalam pembuatan pedal brake menggunakan proses drawing terdapat potensi cacat yang bisa terjadi akibat besarnya gaya serta tingkat kedalaman cetakan. Analisa draw ability dilakukan untuk mengetahui seberapa besar kedalaman proses drawing sebelum benda kerja mengalami kegagalan dengan menghitung nilai Limiting Drawing Ratio (LDR) dan rata-rata plastic strain ratio (Ravg). Simulasi dilakukan untuk mengetahui parameter seperti gaya pembentukan, jumlah energi yang digunakan beserta potensi cacat yang timbul pada pedal brake seperti earing dan kegagalan pada saat melakukan proses drawing. Dari hasil perhitungan LDR sebesar 1,028 dan Ravg sebesar 2,8 untuk jenis material ST-37 menunjukkan bahwa kemampuan draw ability yang rendah dengan gaya pembentukan maksimum sebesar 92,8 kN dan energi yang diserap sebesar 0,69 kJ. Nilai Ravg sebesar 1,2 untuk jenis material ST-37 cukup besar sehingga potensi terjadinya earing tidak terlalu nampak untuk proses drawing. Perbandingan antara analisa teoritis dan simulasi memiliki error sebesar 6% sehingga hasil masih dapat dikatakan valid.
Kata Kunci
Teks Lengkap:
PDFReferensi
Buku Pedoman PT. PINDAD (PERSERO). 1992. Bandung.
Boljanovic, Vukota. 2004. Sheet Metal Forming Processes and Die Design. New York: Industrial Press Inc.
Rashmi Dwivedia, Geeta Agnihotrib. 2017. Study of Deep Drawing Process Parameters. Materials Today: Proceedings 4:820–826
DIN standard 8584: Fabricating process tensile - compressive forming.
Sajjad Izadpanah, Seyed Hadi Ghaderi, Mahdi Gerdooei. 2016. Material parameters identification
procedure for BBC2003 yield criterion and earing prediction in deep drawing. International Journal
of Mechanical Sciences 115-116 : 552–563.
Banabic D. 2010. Sheet metal forming processes. First Romania: Springer.
Alexey Vishtal, Elias Retulainen. 2012. Deep-Drawing of Paper and Paperboard: The Role of
Material Properties. Bio Resources. 7: 4424-4450.
M. El Sherbiny an. El. 2014.Thinning and residual stresses of sheet metal in the deep drawing process. Materials and Design 55: 869–879.
R.L. Whiteley. 1960. The Importance of directionality in drawing quality sheet steel. Trans. ASM 52: 154-164.
D.-K. Leu. 1997. Prediction of the limiting drawing ratio and the maximum drawing load in the cup
drawing. International journal Mechanical Science. 37 (2) : 201-213.
S. Kobayashi. 1989. Metal Forming and Finite element Methode. Oxford University Press. New York. pp.279-325
Mikell P. Groover. 2010. Fundamentals Of Modern Manufacturing; Materials, Processes, and Systems 4th edition. John Wiley & Sons, Inc. ISBN 978-0470-467002.
Lange, K. 1985. Metal forming handbook. McGraw Hill.
Kalpakjian, Serope, Schimid, Steven R. 2009. Manufacturing Engineering and Technology Ed 6th SI Units. Singapore: Prentice Hall
DOI: https://doi.org/10.24176/simet.v9i1.1947
Refbacks
- Saat ini tidak ada refbacks.
Indexed by:



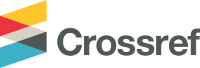
Simetris : Jurnal Teknik Mesin, Elektro dan Ilmu Komputer is licensed under a Creative Commons Attribution-NonCommercial-ShareAlike 4.0 International.
Dedicated to:
